Discover the recent advances in the application of AI to industrial infrastructures.
Overview of Predictive maintenance of pumps in civil infrastructure using AI
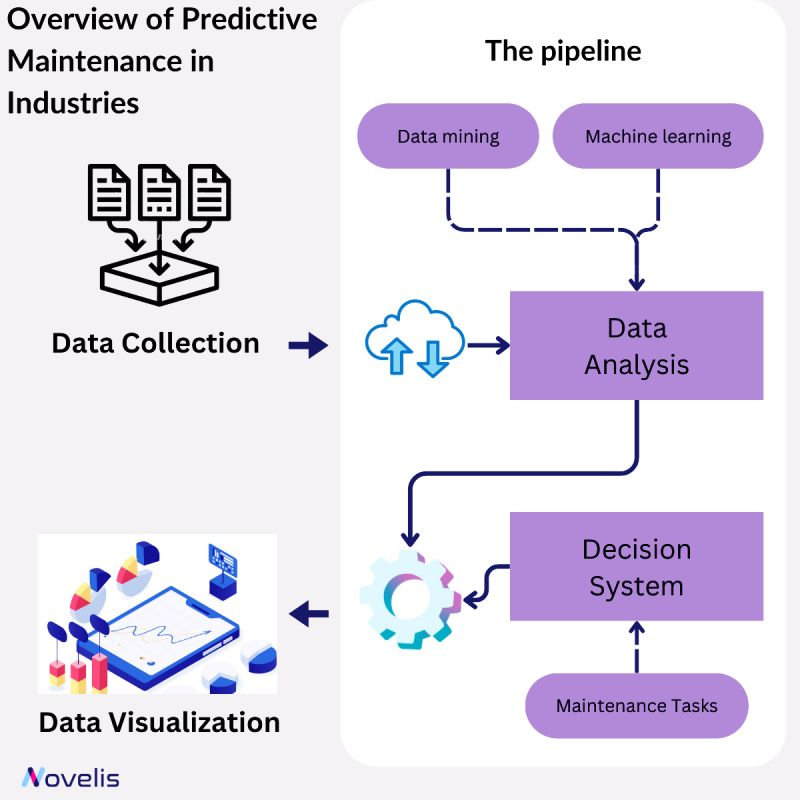
Predictive maintenance (PdM) is a proactive maintenance strategy that leverages data-driven analysis, analytics, artificial intelligence (AI) methods, and advanced technologies to predict when equipment or machinery is likely to fail. An example of predictive maintenance using AI techniques is in civil infrastructure, particularly in the upkeep of pumps.
Three main maintenance strategies are applied to pumps in civil infrastructure: corrective maintenance, preventive maintenance, and predictive maintenance (PdM). Corrective maintenance involves diagnosing, isolating, and rectifying pump faults after they occur, aiming to restore the failed pump to a functional state. Preventive maintenance adheres to a predefined schedule, replacing deteriorated pump parts at regular intervals, irrespective of whether they require replacement. In contrast, to overcome the drawbacks of corrective and preventive maintenance approaches, PdM utilizes data-driven analysis. The process involves continuous monitoring of real-time data from machinery. By employing sensors to gather information like vibration, temperature, and other relevant metrics, the system establishes a baseline for normal operational conditions. Machine learning algorithms then analyze this data, identifying patterns and anomalies indicative of potential issues or deterioration.
A cutting-edge advancement in technology is the ADT-enabled Predictive Maintenance (PdM) framework designed specifically for Wastewater Treatment Plant (WWTP) pumps.
Why is this essential? This technology is important because predictive maintenance of pumps in civil infrastructure, powered by AI, prevents unexpected failures. It enhances system reliability, reduces downtime, and optimizes resource allocation. Detecting issues early through data-driven analysis ensures efficient and resilient operations, which is crucial for the functionality of vital infrastructure components.
LCSA – Machine Learning Based Model
Artificial Intelligence for Smarter, More Sustainable Building Design
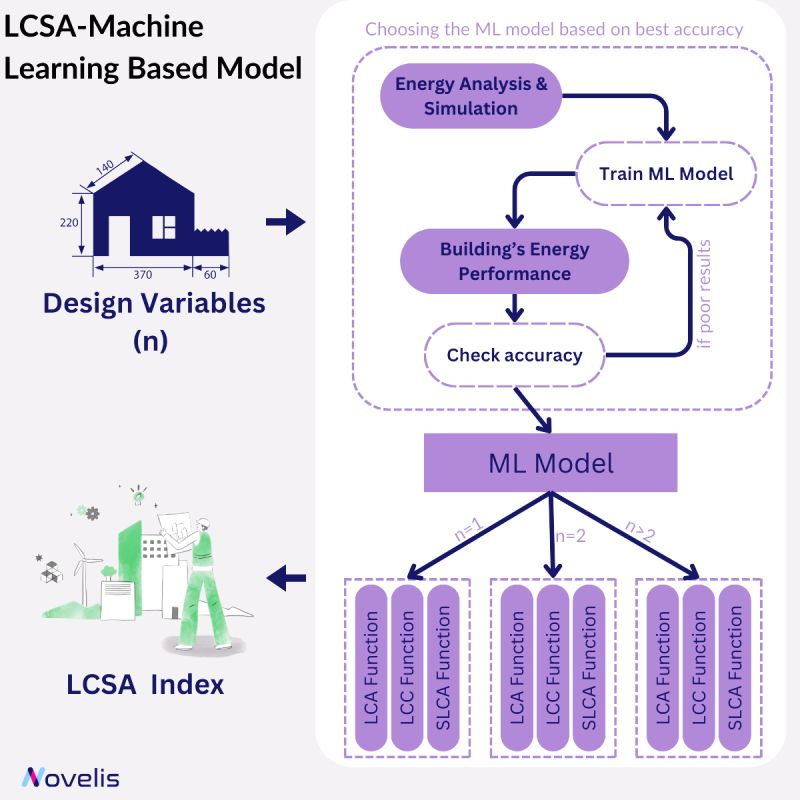
In the last couple of years, the field of artificial intelligence (AI) has had an influence on a great deal of fields from healthcare (check out our posts from last month! 😉), to finance, and even construction!
This month our theme is AI for industrial infrastructures. A large component of industrial infrastructures is the construction of physical infrastructures likes roads, bridges, sewage systems and buildings. This post seeks to tackle AI applications in the construction of buildings. Specifically, we take a deeper look into how AI and machine learning (ML) can help towards designing more sustainable homes and buildings in the future, as well as re-assessing the environmental impacts of existing buildings.
One technique in combatting the negative environmental impacts of the construction industry is to assess the impact of a project before hand, using the Life Cycle Sustainable Assessment (LCSA) approach. The latter takes into account a building’s environmental (Life Cycle Assessment, LCA), economic (Life Cycle Costing, LCC), and social (Social Life Cycle Assessment, SLCA) performance throughout the whole life cycle of a building and gives a better indication of the sustainability of a project.
With the use of an ML model (the best one might differ depending on the project), the building’s energy performance can be predicted and can further help determine the (possibly very complicated) functions for the LCA, LCC and SLCA indexes. The typically tedious and lengthy task of computing the LCSA thus becomes significantly more straightforward.
Why is this essential? This methodology allows for not only the faster assessment and rejection of projects that have unfavourable short and long-term impacts, but the quicker acceptance of better and more sustainable building designs for a greener future!
Smart Quality Inspection
AI-Based Quality Inspection for Manufacturing
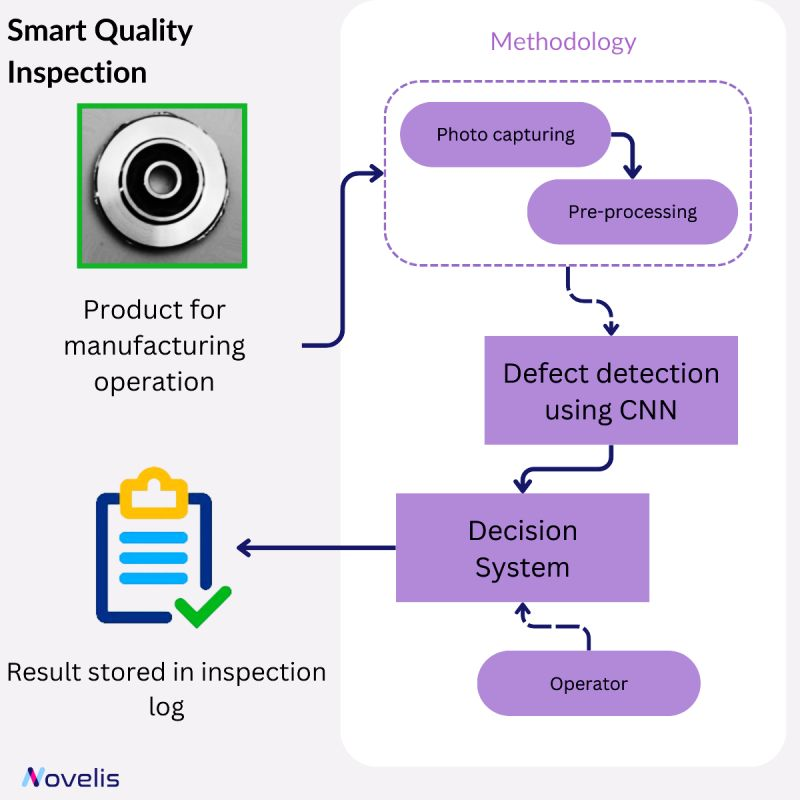
Quality inspection is one of the critical processes to ensure an optimal and low-cost manufacturing system. Human-operated quality inspection accuracy is around 80%. An AI-based approach could boost the accuracy of the visual inspection process up to 99.86%. Find out how:
The Smart Quality Inspection (SQI) process consists of six stages. The first stage involves bringing the product to the inspection area from the assembly line and placing it in a designated location. A high-quality camera captures images of the item during inspection. The lighting conditions and distance from the product are adjusted based on size and camera equipment, and any necessary image transformation is done at this stage. The next stage involves using a custom Convolutional Neural Network (CNN) architecture to detect defects during the AI-based inspection. The CNN architecture can handle different types of images with minimal modifications, and it is trained on images of defective and non-defective products to learn the necessary feature representations. The defect detection model is integrated into an application used on the shop floor to streamline the inspection process. During the inspection, the operator uses the defect detection algorithm, and based on the results, a decision is made on whether to accept or reject the product. The results of the inspection process are input into the SQI shop floor application and are automatically stored in a spreadsheet. This makes it easier for the team to track and analyze the results.
Why is this essential? This technology is crucial for monitoring the manufacturing environment’s health, preventing unforeseen repairs and shutdowns, and detecting defective products that could result in significant losses.